An Overview Of Low Volume Injection Molding
Injection molding is a popular manufacturing process used to create various plastic products. While manufacturers use traditional injection molding for producing large parts, they specifically design low volume injection molding for smaller production runs. This method offers numerous advantages, including lower costs and quicker turnaround times. This post will look in-depth at low volume injection molding, including its definition, process, materials, and applications.
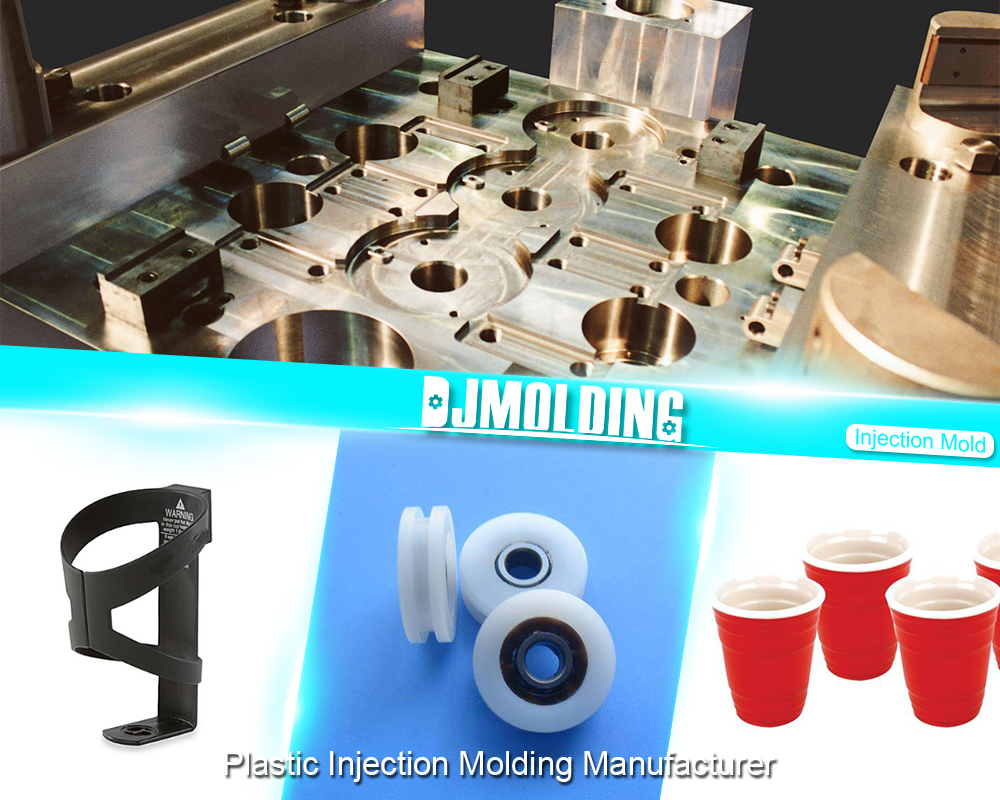
WHAT IS LOW VOLUME INJECTION MOLDING?
Definition and Explanation
Low volume injection molding is a manufacturing process that uses injection molding technology to produce small quantities of plastic parts. This method is ideal for businesses that need to make small pieces quickly and cost-effectively. You can use low volume injection molding for various plastic parts, including housings, covers, and enclosures.
Benefits of using low volume injection molding:
- Cost-effectiveness: Low volume injection molding is cost-effective for producing small parts.
- Quick turnaround time: The process is faster than traditional injection molding, making it ideal for businesses that need to create pieces quickly.
- High-quality parts: Low volume injection molding has high-quality parts that are accurate and consistent.
PROCESS OF LOW VOLUME INJECTION MOLDING
Low volume injection molding is a manufacturing process used to produce small quantities of plastic parts quickly and cost-effectively. The process involves several steps: design, mold creation, material selection, injection molding, cooling, ejection, and finishing. Here’s a closer look at each stage:
Design
The first step in low volume injection molding requires designing a 3D model for producing the part. You can create the technique using computer-aided design (CAD) software or scanning existing features. The design must be precise and detailed to ensure the final product meets the specifications.
Mold creation
Once the design is complete, a mold is created based on the 3D structure. Typically, manufacturers use metal to create the mold, which consists of two halves that fit together to form the shape of the part they intend to produce.
Material selection
The material used for low volume injection molding is selected based on the specific requirements of the part. Manufacturers consider strength, durability, and temperature resistance when determining the material.
Injection molding
The selected material is heated to molten and then injected into the mold. The molten plastic is injected at high pressure to ensure that it fills the entire mold and forms the shape of the part.
Cooling
After injecting the plastic into the mold, manufacturers cool it to solidify it. Cooling is critical to ensure the plastic retains its shape and does not warp or deform.
Injection
Once the plastic solidifies, manufacturers inject the finished part from the mold. Manufacturers separate the two halves of the mold and remove the piece from it.
Finishing
After ejecting the part from the mold, we complete any necessary finishing touches. To enhance the appearance and functionality of the item, you can trim any excess material, apply a fresh coat of paint or coating, or add essential labels or markings.
The low volume injection molding process is cost-effective and efficient for producing small plastic parts. By following the steps of design, mold creation, material selection, injection molding, cooling, ejection, and finishing, manufacturers can produce high-quality parts quickly and with high precision.
Equipment used in the process
- Injection molding machine
- Mold
- Material feeder
- Cooling system
- Ejection system
- MATERIALS USED IN LOW VOLUME INJECTION MOLDING
Types of materials commonly used:
- Thermoplastics are the most frequently used materials for low volume injection molding. Examples include polystyrene, polypropylene, and ABS.
- Liquid silicone rubber (LSR): Manufacturers use LSR for parts that require flexibility, durability, and high-temperature resistance.
- Polyurethane (PU): Manufacturers use PU for parts that need flexibility and impact resistance.
- Thermosets: Manufacturers use thermosets for features that require high-temperature resistance.
- Advantages and disadvantages of each material:
- Thermoplastics: Advantages include flexibility, durability, and ease of use. Disadvantages include lower temperature resistance and susceptibility to warping.
- Liquid silicone rubber (LSR): Advantages include flexibility, durability, and high-temperature resistance. Disadvantages include higher costs and longer curing times.
- Polyurethane (PU): Advantages include flexibility and impact resistance. Disadvantages include lower temperature resistance and higher prices.
- Thermosets: Advantages include high-temperature resistance and durability. Disadvantages include longer curing times and difficulty in recycling.
APPLICATIONS OF LOW VOLUME INJECTION MOLDING
Low volume injection molding has a wide range of applications across various industries. This manufacturing process is beneficial for producing small quantities of plastic parts quickly and cost-effectively. Here are some examples of products made with low volume injection molding and the industries that commonly use this method:
Medical equipment components
Medical equipment requires precise and high-quality parts to ensure the safety and effectiveness of medical procedures. Low volume injection molding can produce these parts with tight tolerances and consistent quality, making it a popular choice in the medical industry.
Electronic housings and covers
The electronics industry requires custom housings and covers to protect and house electronic components. Low volume injection molding can produce these parts with high precision, making it ideal for producing electronic housings and covers in small quantities.
Automotive parts
The automotive industry requires various plastic parts for vehicles’ interior and exterior. Low volume injection molding can produce these parts quickly and efficiently, making it a cost-effective method for producing small quantities of automotive parts.
Consumer goods
Consumer goods such as toys, kitchenware, and household appliances often require custom plastic parts. Low volume injection molding can produce these parts in small quantities, allowing manufacturers to test and refine their designs before moving to mass production.
Industries that use this method
Low volume injection molding is used in various industries because it produces high-quality plastic parts in small quantities quickly and cost-effectively. Here are some of the industries that commonly use this method:
Medical
Low volume injection molding is popular in the medical industry due to its ability to produce precise and high-quality medical equipment components.
Automotive
The automotive industry requires various plastic parts, and low volume injection molding is a cost-effective way to produce small quantities of these parts.
Consumer goods
Manufacturers of consumer goods such as toys, kitchenware, and household appliances use low volume injection molding to produce custom plastic parts.
Electronics
The electronics industry requires custom housings and covers to protect and house electronic components, making low volume injection molding a popular choice.
Aerospace
The aerospace industry requires lightweight and durable plastic parts, making low volume injection molding an attractive option due to its ability to produce high-quality parts quickly and efficiently.
Industrial
Various industries utilize low volume injection molding to manufacture equipment components and produce custom parts for machinery.
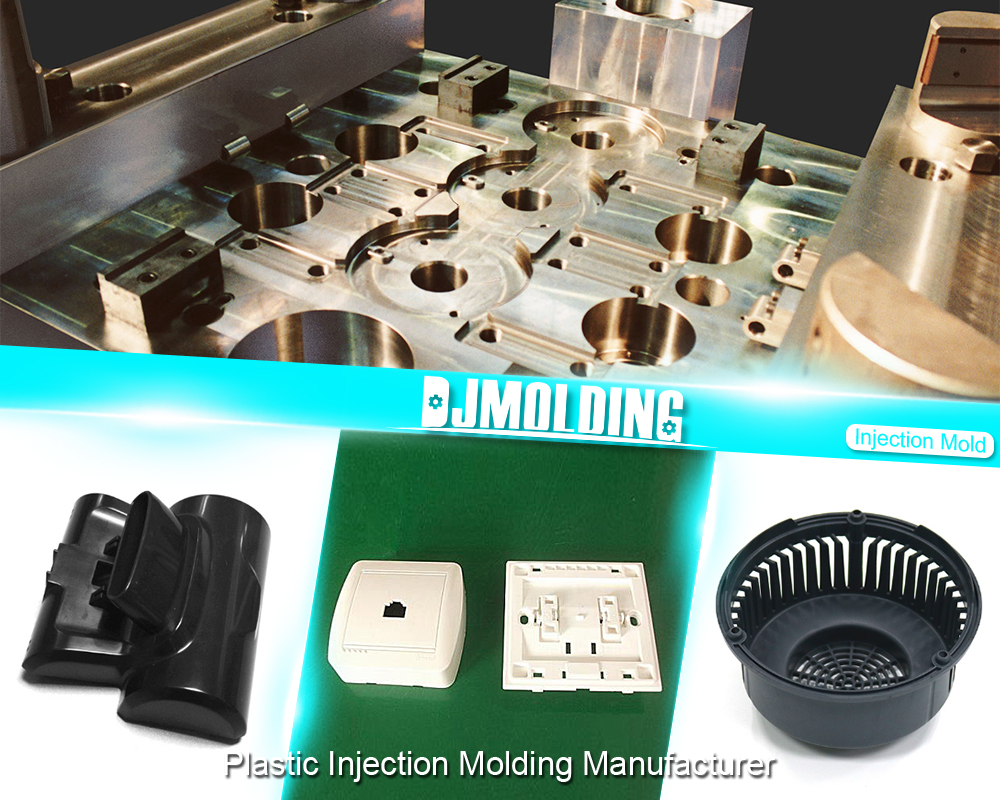
CONCLUSION
Low volume injection molding is a cost-effective and efficient manufacturing process for businesses that need to produce small quantities of plastic parts. By understanding the benefits, processes, and materials used in this method, companies can make informed decisions about the right choice for their needs. It is vital to use associated keywords to optimize content for search engines and ensure that the blog post reaches a broader audience. With its numerous advantages and diverse applications, low volume injection molding is a valuable tool for businesses looking to produce small quantities of high-quality plastic parts.
For more about an overview of low volume injection molding,you can pay a visit to Djmolding at https://www.djmolding.com/low-volume-injection-molding/ for more info.
Article Original From: https://www.djmolding.com/an-overview-of-low-volume-injection-molding/