All You Need to Know About Plastic Injection Molding
Plastic injection molding is a widely used manufacturing process to produce complex plastic components. This blog post will discuss the basics of plastic injection molding, its function, applications, advantages, and disadvantages.
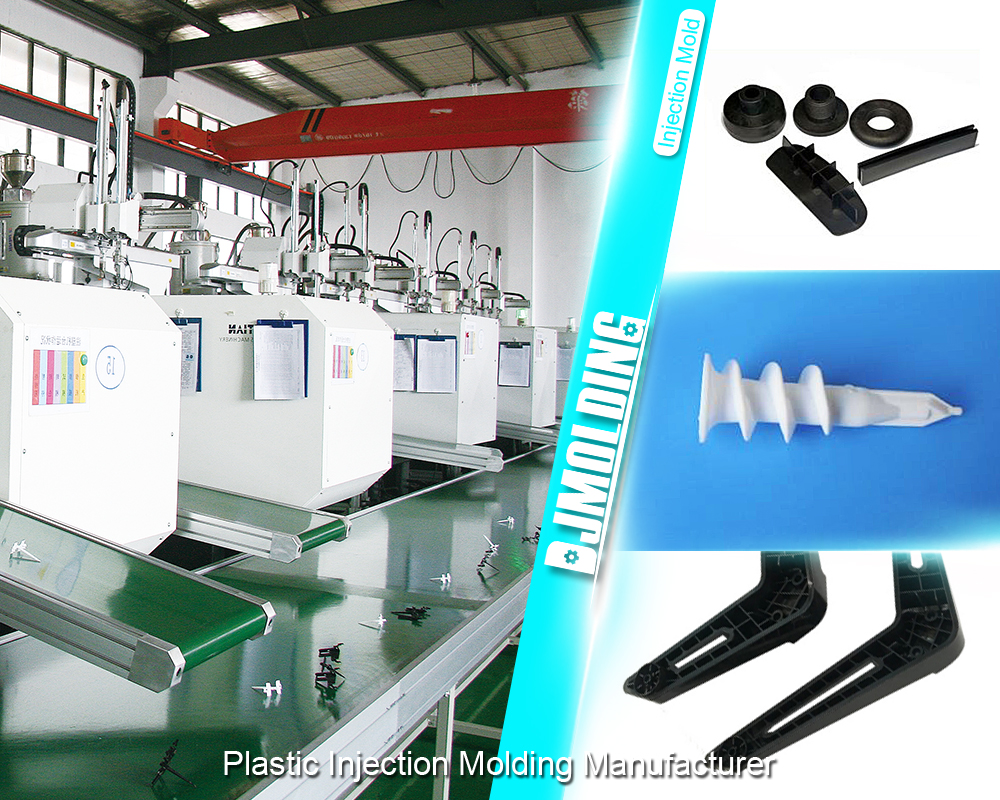
Plastic Injection Molding:
Plastic injection molding is one of the most popular manufacturing methods for producing high-quality plastic products in large quantities. Various industries, such as automotive, medical, packaging, and consumer goods, use injection molding to manufacture their products. The process involves melting plastic pellets and injecting them into a mold under high pressure. The plastic then cools and solidifies, forming the mold cavity. In this blog post, we will dive into the details of the plastic injection molding process.
The Plastic Injection Molding Process
Plastic injection molding is a complex process that involves multiple steps. Here are the basic steps involved in the plastic injection molding process:
Mold Design
The first step in the process is designing the mold. The first step in the process is to develop the mold using computer-aided design (CAD) software, which helps to create a 3D model of the component. The mold is made based on this design using steel or aluminum.
Material Selection
The next step is selecting the material for the component. Thermoplastics, which can melt and reshape multiple times, are the most commonly used materials for plastic injection molding. The material selected should be suitable for the intended application.
Heating and Melting
Once the design team creates the mold and selects the appropriate material, the injection molding machine heats and melts the plastic pellets. The injection molding process controls the temperature carefully to ensure even melting of the material.
Injection
We then inject the melted plastic into the mold cavity under high pressure. The pressure ensures that the material fills the entire niche and takes the shape of the mold.
Cooling and Ejection
The plastic is then allowed to cool and solidify, taking the shape of the mold cavity. Once the plastic cools, the injection molding machine opens the mold and ejects the component.
Uses for Plastic Injection Moulding
Plastic injection molding is used in various industries to produce different components. Here are some of the most common applications of plastic injection molding:
- Vehicle Industry: Various industries use plastic injection molding to produce a variety of components, such as automotive dashboards, bumpers, and interior trims.
- The medical sector: Plastic injection molding produces medical devices like syringes, inhalers, and surgical instruments.
- Packaging Industry: Plastic injection molding produces packaging components like bottle caps, containers, and closures.
- Consumer Goods Industry: Plastic injection molding produces various consumer goods, such as toys, electronics, and household appliances.
Advantages of Plastic Injection Molding
Plastic injection molding is a widely used manufacturing process that offers several advantages over other manufacturing methods. The process involves injecting molten plastic into a mold cavity, which cools and solidifies to form a high-quality component. Here are some of the advantages of plastic injection molding.
High Efficiency
Plastic injection molding is a highly efficient process that can quickly produce high volumes of components. It is an automated process with hundreds or even thousands of features rapidly, making it ideal for large-scale production runs. Additionally, the process can be optimized to minimize cycle time, further improving efficiency.
Consistency and Precision
Plastic injection molding produces components consistent in size and shape with high precision. The mold cavity ensures that the machine makes the element with the desired dimensions and that the process is highly repeatable. The consistent quality produced by plastic injection molding is essential for applications where precise measurements are critical, ensuring that the components produced will have consistent quality.
Versatility
Plastic injection molding can produce components in various sizes and shapes. Designers can create molds with features with complex geometries, such as thin-walled parts, which may be difficult or impossible to produce using other methods. Additionally, the process can use various plastic materials, including engineering-grade resins, which can be selected based on the desired properties of the component.
Cost-Effective
Plastic injection molding is a cost-effective process for producing high volumes of components. The initial cost of designing and manufacturing the mold can be high, but the cost per component decreases as the volume of production increases. Additionally, the process can be automated, which reduces labor costs and improves efficiency. The minimal material waste also helps to reduce costs, as any excess material can be recycled and used in future production runs.
Minimal Material Waste
Plastic injection molding produces minimal material waste, as any excess material can be recycled and used in future production runs. Plastic injection molding is more efficient than other manufacturing methods because it melts and injects only the required amount of material into the mold cavity, reducing waste. Any excess material is typically collected and reused, which reduces waste and improves sustainability.
Most significant disadvantages
Manufacturers widely use plastic injection molding for its advantages but must consider some significant disadvantages. This section will discuss the most important disadvantages of plastic injection molding.
High Initial Investment
One of the main disadvantages of plastic injection molding is the high initial investment required to create the mold. The mold design and creation process can be costly, particularly for complex designs or large molds. The cost of the mold can be a barrier to entry for small businesses or startups, making it difficult for them to compete with larger companies that can afford the high investment.
Limited Design Flexibility
The mold limits the component’s design, which means that making changes to the procedure can be difficult and expensive. Making frequent changes to the mold can be a significant disadvantage as it requires additional time and money for each modification. This limitation in design flexibility can be particularly challenging for products that require frequent updates or customization.
Production Time
Another disadvantage of plastic injection molding is that the process can take several weeks, from design to production. The time required for mold design and creation, material preparation, and production can make it challenging to meet fast turnaround times. Modifying the mold can be a significant disadvantage for companies that require quick production times or face short product life cycles.
Environmental Impact
The plastic injection molding process can harm the environment. The process requires using fossil fuels to heat and melt the plastic, contributing to greenhouse gas emissions. Additionally, the process can generate waste in excess plastic and energy use, harming the environment.
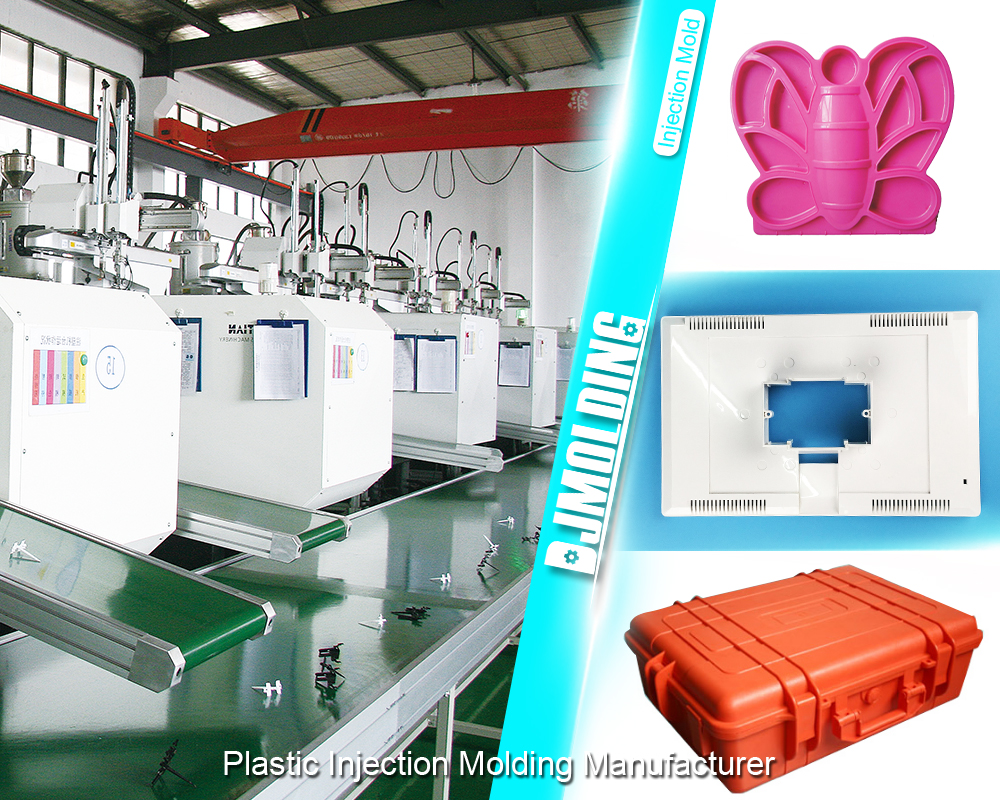
CONCLUSION
In conclusion, plastic injection molding is a reliable and efficient manufacturing process for producing high-quality plastic products. Its advantages, such as consistency, precision, and cost-effectiveness, make it a popular choice for various industries. However, its disadvantages, such as the high initial investment and limited design flexibility, should also be considered. Plastic injection molding is a valuable technology that has revolutionized the manufacturing industry. As technology advances, plastic injection molding will likely continue to evolve and improve, becoming even more efficient, cost-effective, and environmentally friendly.
For more about plastic injection molding,you can pay a visit to Djmolding at https://www.djmolding.com/ for more info.
Original From: https://www.djmolding.com/all-you-need-to-know-about-plastic-injection-molding/